„Wer heute nicht automatisiert, hat schon verloren“
Interview mit Thomas Pomp, Geschäftsführer der FAMAG-Werkzeugfabrik GmbH & Co. KG
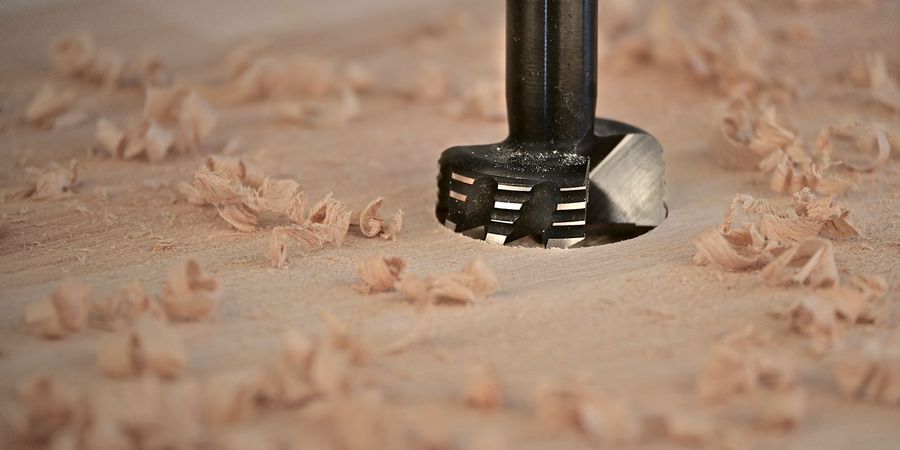
Wirtschaftsforum: Herr Pomp, im Jahr 1990 sind Sie in die FAMAG-Werkzeugfabrik GmbH & Co. KG eingetreten – und haben schon kurz danach wichtige Innovationen angestoßen!
Thomas Pomp: Ich kam frisch nach meiner Ausbildung zum CNC-Programmierer in das Unternehmen, zu einem Zeitpunkt, als dort eigentlich keinerlei Innovationen mehr umgesetzt wurden: Der Maschinenpark war veraltet, das Personal durchweg kurz vor der Verrentung. Dank meiner CNC-Kenntnisse habe ich jedoch direkt erkannt, wie man diese neuen Techniken zielführend einsetzen konnte, um die Kernkompetenzen von FAMAG nachhaltig zu schärfen und einen echten Mehrwert im Markt zu schaffen. Schon wenig später konnten wir die ersten Patente auf den Weg bringen und für FAMAG fing wieder ein Licht an zu leuchten.
Wirtschaftsforum: Bereits 1991 schlug die Geburtsstunde des Bormax – bis heute eines der beliebtesten Produkte im Portfolio von FAMAG.
Thomas Pomp: Ich hatte damals die Idee, den klassischen Forstnerbohrer nachhaltig zu verbessern. Unser Ziel war es, an unserem Standort den besten Bohrer herzustellen, den man auf dem Markt bekommen kann – daran haben wir lange geforscht und getestet. Schließlich ist es uns gelungen, mit dem Bormax weltweit Maßstäbe zu setzen – er hat viel längere Standzeiten, arbeitet präziser und kann wesentlich leichter eingesetzt werden. Zudem ist er ein Produkt fürs Auge: Man erkennt auf den ersten Blick, dass er nicht auf die einfache Art hergestellt wurde. Unsere Erfahrung zeigt: Wer einmal mit dem Bormax ein Loch gebohrt hat, will dafür kein anderes Werkzeug mehr in die Hand nehmen. Das bestätigen uns auch regelmäßig Handwerker auf der Walz, die unseren Betrieb besuchen.
Wirtschaftsforum: Liegt darin auch ein wichtiges Alleinstellungsmerkmal angesichts des Wettbewerbs aus Fernost, wo mit ganz anderen Kostenstrukturen gefertigt werden kann?
Thomas Pomp: In China gibt es eine ganze Stadt, in der einzig und allein Bohrer hergestellt werden. Die Mengen, die auf den Weltmarkt fließen, sind also in der Tat enorm. Noch dazu kosten die dort vielfach eingesetzten Maschinen und Anlagen bisweilen nur ein Fünftel der hiesigen Preise. Trotzdem können sich viele ostasiatische Erzeugnisse mittlerweile auch in qualitativer Hinsicht sehen lassen. Das, was diese Länder technologisch zu leisten imstande sind, verdient ohne Frage unsere Anerkennung. Trotzdem wird unser unumwundenes Qualitätsversprechen auch perspektivisch unser wichtigstes Alleinstellungsmerkmal im Markt bleiben – denn dadurch konnten wir uns überhaupt erst durchsetzen. Die Qualität, die wir herstellen, kann man weder mit Handarbeit noch mit billigeren Anlagen erreichen. Mit unseren modernsten 5-Achs-Fräs- und Schleifmaschinen sowie unserem hohen Automatisierungsgrad setzen wir konsequent auf die besten technischen Lösungen, die im Markt zur Herstellung unserer Werkzeuge zur Verfügung stehen.
Wirtschaftsforum: Mittlerweile bietet FAMAG seine Kompetenz als Automatisierungsexperte auch anderen Unternehmen an – wie kam es zu dieser Entwicklung?
Thomas Pomp: Unser umfassender Einsatz von Robotern, durch die etwa eine unserer Schichten komplett mannlos besetzt werden kann, ist ein entscheidender Grund dafür, dass wir dem Wettbewerb aus dem Ausland nachhaltig standhalten können. Man kann noch so tolle Werkzeuge erfinden – wenn man sie nicht wirtschaftlich profitabel herstellen kann, wird man nicht erfolgreich sein. Uns ist klar, dass auch viele andere fertigungsintensive Unternehmen in Deutschland vor ähnlichen Herausforderungen stehen – und wir sind überzeugt, dass wir sie dank unserer langjährigen Erfahrung auf ihrem Weg wirkmächtig unterstützen können. Deshalb bauen wir seit einigen Jahren auch robotergestützte automatisierte Maschinen, die mehrere Arbeitsgänge miteinander verbinden und so nachhaltig zur Optimierung der jeweiligen Fertigungsumgebung beitragen.
Wirtschaftsforum: Wie blicken Sie perspektivisch auf den Fertigungsstandort Deutschland?
Thomas Pomp: Als ich 1990 zu FAMAG kam, sagte man mir, ich müsse verrückt sein, in diese Werkzeugproduktion in Deutschland zu investieren, das mache man doch heute alles in China. Entgegen diesem Trend habe ich in Deutschland eine hochmoderne Produktion aufgebaut. Diese Bohrer in einer Spitzenqualität herzustellen, war und ist nicht preiswert – aber die Rechnung ging voll auf. Sicherlich sind die hohen Energiepreise in Deutschland heute ein großes Problem – für viele unserer Lieferanten und befreundeten Unternehmen noch weit mehr als für uns. Das müssen wir sachorientiert und gesamtwirtschaftlich lösen. Denn klar ist: Wir sind nicht mehr auf einer einsamen Insel, sondern Teil eines globalen Wettbewerbs!