60% leichter als Stahl: Die Zukunft liegt im Leichtbau
Interview mit Jürgen Enz, Geschäftsführer der ACE Advanced Composite Engineering GmbH
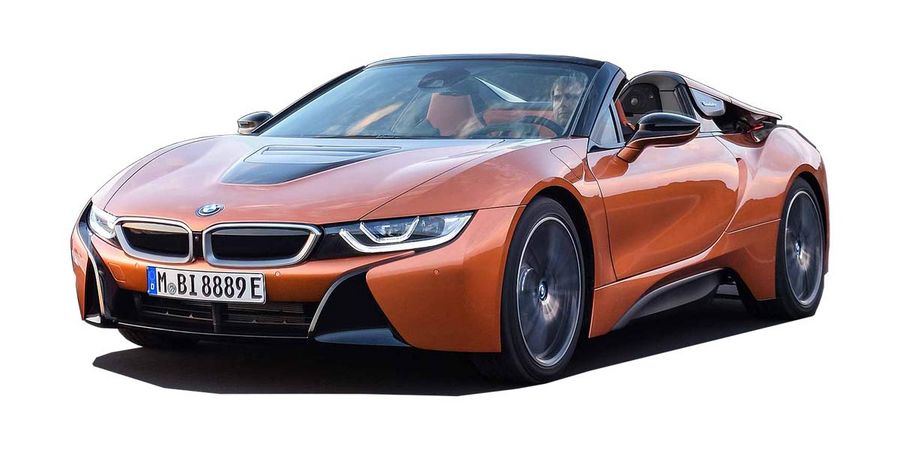
Wirtschaftsforum: Herr Enz, wie kam es zur Gründung von ACE?
Jürgen Enz: Als Luft- und Raumfahrtingenieur war ich 13 Jahre bei Dornier tätig. Dornier ging später in der DaimlerChrysler Aerospace und diese in EADS und Airbus auf. Bei Dornier hatte ich mit dem Leichtbau mit Faserverbundwerkstoff, insbesondere Kohlenstofffasern, zu tun. Vor etwa 30 Jahren haben wir das Thema im DaimlerChrysler Konzern auch in den Automobilbau getragen. Bei EADS war das Automotivethema dann nicht mehr gefragt. Als Leiter der entsprechenden Business Unit habe ich mich daher 2001 mit zwei Mitgesellschaftern, den Herren G. Erdl und P. Gröschl, zu einem Management-Buy-out entschlossen und ACE als Spin-off aus der EADS heraus gegründet. Wir haben mit zwölf Mitarbeitern begonnen. Heute sind wir rund 250 und erwirtschaften einen Jahresumsatz von 35 Millionen EUR.
Wirtschaftsforum: Wie hat sich ACE seit 2001 entwickelt?
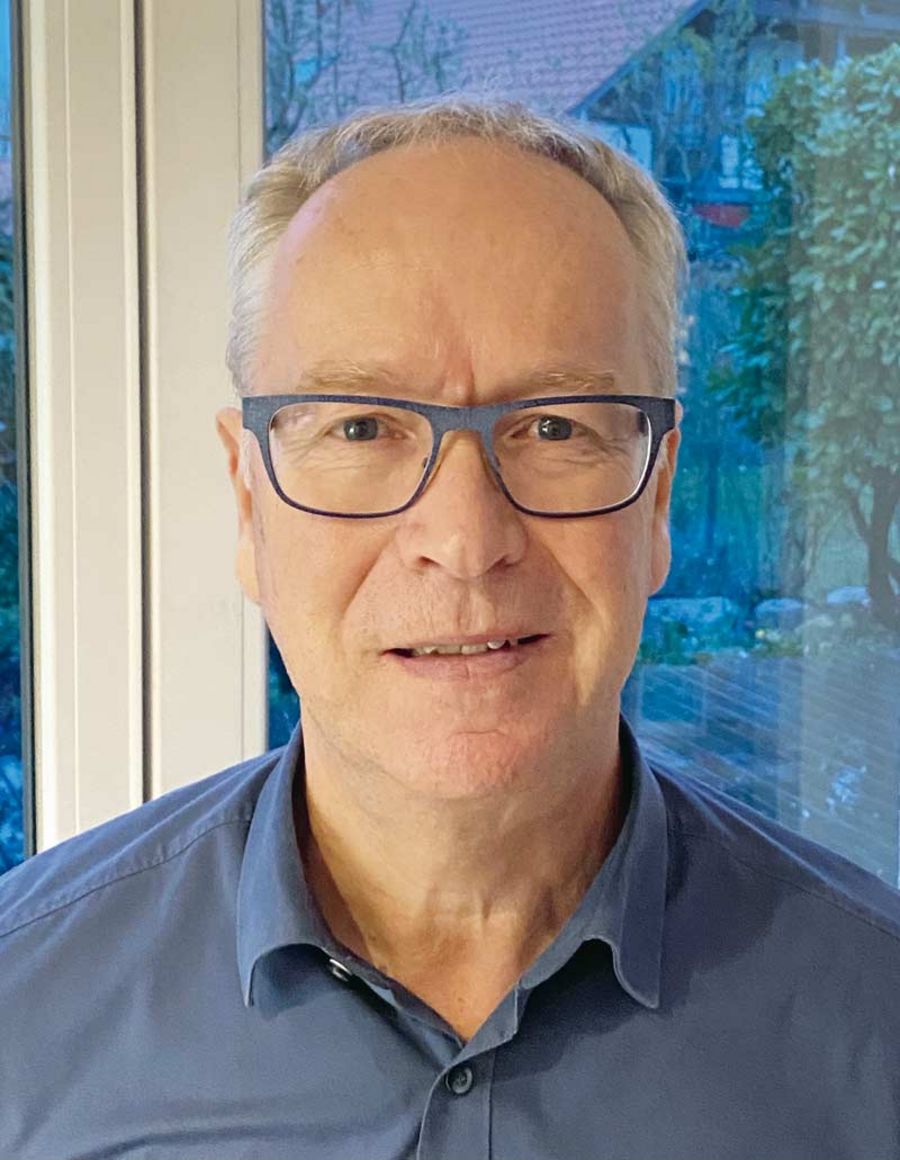
Jürgen Enz: Zu Beginn haben wir uns mit der Entwicklung von Leichtbauteilen im Automobil- und Luftfahrtmarkt beschäftigt. Nach kurzer Zeit haben wir einen Prototypenbau etabliert und sind dann in die Serienfertigung eingestiegen. Hier haben wir uns auf die RTM-Technik spezialisiert, die hohe Stückzahlen in kurzer Zeit ermöglicht. Die Kohlefaserteile können damit in einem Takt von fünf Minuten hergestellt werden.
Wirtschaftsforum: Was macht Kohlefasern für den Automobil- und Luftfahrtbau so wertvoll?
Jürgen Enz: Die Gewichtseinsparung gegenüber Stahl liegt bei durchschnittlich 60%, gegenüber Aluminium bei 40%. Kohlefaser hat außerdem sehr gute mechanische Eigenschaften und funktionale Vorteile. Neue Flugzeuggenerationen wie die Airbus A350 oder Boeing 787 bestehen deshalb nahezu komplett aus Kohlefaser.
Wirtschaftsforum: Welche Produkte stellen Sie im Einzelnen her?
Jürgen Enz: Im Automobilbau fertigen wir Komponenten der Karosserie wie Motorhauben, Heckklappen, Verdeckkastendeckel für Cabrios oder Türen, aber auch High-End bis zum Monocoque, also ein aus einem Stück gefertigtes Strukturbauteil, für Kleinserienanwendungen. Dazu kommen Komponenten des Antriebsstranges. Im Bereich der Luftfahrt fertigen wir kleinere Teile für Airbus wie Fensterrahmen für die A350. Das sind wichtige Strukturbauteile, weil sie den Druckrumpf um das Fensterloch herum verstärken müssen. In unserem dritten Bereich Industrieanwendungen bieten wir zum Beispiel Feeder-Systeme für Transferpressen in Pressenstraßen.
Wirtschaftsforum: Wie wichtig sind denn Leichtbauteile für E-Fahrzeuge?
Jürgen Enz: Das Thema Safecar ist auch bei alternativen Antrieben ganz wesentlich. Beim Elektroauto ist die Gewichtskompensation im Strukturbereich noch dringender notwendig, da Batteriegewichte von bis zu einer halben Tonne hinzukommen. Auch bei den Batterieboxen, die die Batterie schützen müssen, ist Faserverbund ein Thema.
Wirtschaftsforum: Für welche Kunden arbeiten Sie?
Jürgen Enz: Hauptsächlich sind wir im Bereich der sportiven und hochwertigen Automobile wie Lamborghini, Porsche, Aston Martin, Audi Sport oder Mercedes AMG tätig. Zu unseren Kunden gehören weitere europäische und japanische Firmen. Im Flugzeugbau arbeiten wir für Airbus und diverse Tier-1-Zulieferer.
Wirtschaftsforum: Womit hebt sich ACE am Markt ab?
Jürgen Enz: Unser Know-how in der faserverbundgerechten, belastungsorientierten Konstruktion und Berechnung hat nicht jeder Wettbewerber. Wir haben Entwicklung und Serie komplett inhouse. Im Automobilbau sind wir in der Herstellung der Class-A-Oberfläche besonders gut. Mit der RTM-Technik können wir zudem komplexe Bauteile mit Schieberwerkzeugen, also beweglichen Werkzeugelementen, produzieren.
Wirtschaftsforum: Wie sehen Sie die Zukunft Ihres Unternehmens, und welche Themen werden zukünftig von Bedeutung sein?
Jürgen Enz: Mittelfristig werden wir mit Automobil und Luftfahrt weiter gut aufgestellt sein. Im Rahmen der Umweltthemen wird der Leichtbau hier noch wichtiger sein. Wir engagieren uns auch für Leichtbau bei Wasserstofftanks für Lkw und Flugzeuge. Diese Drucktanks mit einem Druck von 300 bis 700 Bar sind heute schon ausschließlich in Faserverbundtechnik hergestellt. Wir sind dabei, Tanksysteme in einem neuen Fertigungsverfahren zu entwickeln. Im Rahmen der Nachhaltigkeit beschäftigen wir uns auch mit der Verarbeitung von Harzsystemen aus nachwachsenden Rohstoffen und damit, wie wir Faserwerkstoffe einer Recyclingkette zuführen können. In Forschungsprojekten zu Recycling und Prozessoptimierung sind wir europaweit aktiv.