Innovation im Maschinenbau: Wie KI die Wartung von Hochdruckanlagen optimiert
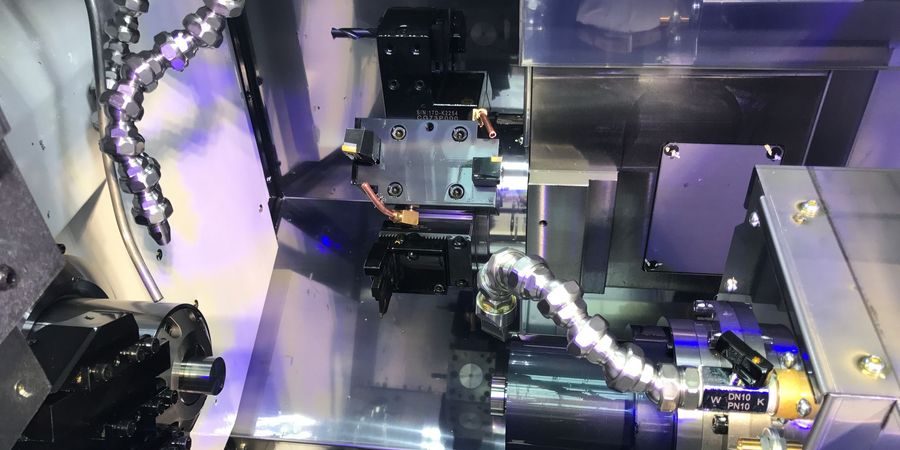
Hochdruckanlagen spielen in diesem Kontext eine zentrale Rolle − insbesondere in Branchen wie der Energieerzeugung, der Automobilfertigung und der chemischen Industrie. Mit zunehmender Komplexität der Maschinen wachsen auch die Herausforderungen, vor allem in Hinblick auf die Wartung.
Hier bietet die Kombination aus Künstlicher Intelligenz und einer vorausschauenden Instandhaltung − auch Predictive Maintenance genannt − vielversprechende Lösungen.
Neue Technologien für alte Herausforderungen
Maschinenstillstände gehören zu den teuersten Risiken für Unternehmen. Die Gründe können vielfältig ausfallen: Überlastung, Materialermüdung oder die Alterung zentraler Komponenten wie Dichtungen und Ventile.
Während die herkömmlichen Wartungsansätze vor allem auf regelmäßigen Inspektionen basieren, setzen moderne KI-Systeme auf datengestützte Prognosen. Mit Hilfe von Sensorik und Machine-Learning-Algorithmen können Fehlerquellen frühzeitig erkannt werden, noch bevor ein Schaden entsteht. Dies minimiert nicht nur Ausfallzeiten, sondern reduziert auch Kosten, die durch ungeplante Reparaturen oder Produktionsunterbrechungen entstehen.
Ein Beispiel für diese Entwicklung ist die Integration smarter Sensoren in Hochdruckanlagen. Diese überwachen kontinuierlich Parameter wie Druck, Temperatur oder Durchflussraten und liefern in Echtzeit Daten an ein zentrales System. Die KI analysiert diese Daten, erkennt Anomalien und kann somit präzise vorhersagen, wann bestimmte Bauteile ausgetauscht oder gewartet werden müssen. Das Ergebnis: eine wesentlich höhere Effizienz und eine längere Lebensdauer der Maschinen.
Hydraulikdichtungen für die Effizienzsteigerung
Eine zentrale Komponente bei der Wartung von Hochdruckanlagen stellen die Hydraulikdichtungen dar. Diese unscheinbaren Bauteile tragen wesentlich zur Funktionsfähigkeit der gesamten Anlage bei, indem sie Flüssigkeiten unter extremen Bedingungen sicher abdichten. Ein Ausfall dieser Dichtungen kann schwerwiegende Konsequenzen haben, da er sowohl den Betrieb stört als auch hohe Reparaturkosten verursacht.
Im Kontext der Predictive Maintenance haben Hydraulikdichtungen für Hochdruckanlagen eine besondere Bedeutung. KI-gestützte Systeme analysieren beispielsweise Verschleißmuster an den Dichtungen und können frühzeitig Signale senden, wenn eine Materialermüdung droht. So lassen sich Schäden vermeiden, bevor sie überhaupt erst entstehen.
Durch die gezielte Kombination aus intelligenten Vorhersagen und rechtzeitiger Wartung wird damit nicht nur die Sicherheit erhöht, sondern auch die Effizienz der gesamten Anlage gesteigert.
Wirtschaftlicher und ökologischer Mehrwert
Die Vorteile von Predictive Maintenance sind nicht nur wirtschaftlicher, sondern auch ökologischer Natur. Indem Bauteile wie Hydraulikdichtungen nicht mehr nach einem starren Zeitplan, sondern vielmehr nach dem tatsächlichen Bedarf ausgetauscht werden, wird der Verbrauch von Ressourcen reduziert. Das schont die Umwelt und senkt gleichzeitig die Betriebskosten.
Darüber hinaus ermöglicht die Digitalisierung des Maschinenbaus eine präzisere Planung von Wartungsintervallen. Die Unternehmen können so die Ersatzteile bedarfsgerecht bestellen, wodurch die Lagerkosten minimiert und die Lieferketten entlastet werden.
Dieser Ansatz trägt maßgeblich dazu bei, nachhaltige und ressourcenschonende Prozesse zu etablieren – ein entscheidender Faktor in Zeiten steigender Energie- und Rohstoffpreise.
Die Herausforderungen bei der Implementierung
Trotz der vielversprechenden Perspektiven stehen die Unternehmen allerdings vor einigen Hürden bei der Einführung von Predictive Maintenance.
Die Integration von KI-Technologie erfordert hohe finanzielle Investitionen in Hard- und Software sowie eine umfassende Schulung der Mitarbeiter. Zudem ist der Erfolg stark von der Qualität der gesammelten Daten abhängig: Ungenaue oder unvollständige Daten können zu fehlerhaften Prognosen führen, was die Akzeptanz der Technologie gefährden könnte.
Ein weiterer Aspekt ist der Datenschutz. Insbesondere in sensiblen Industrien müssen die Unternehmen unbedingt sicherstellen, dass die gesammelten Daten geschützt und nur für den vorgesehenen Zweck verwendet werden.