Made in Germany bleibt gefragt – Wie Kunststoffspritzguss-Hersteller im internationalen Wettbewerb bestehen
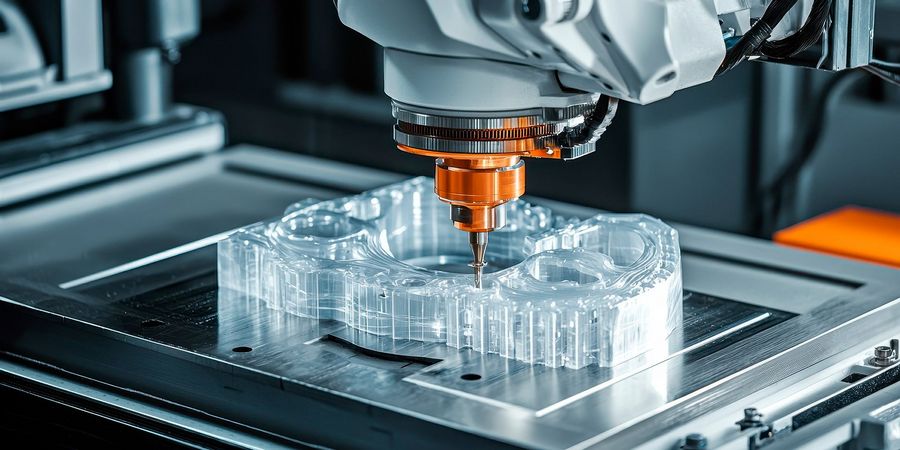
Warum ist Made in Germany im Kunststoffspritzguss relevant?
Das Gütesiegel "Made in Germany" steht in der Kunststoffbranche für höchste Qualitätsstandards und Zuverlässigkeit. Internationale Kunden wählen bewusst deutsche Anbieter, wenn Qualität, Präzision und Langlebigkeit entscheidend sind. Diese Reputation hat sich über Jahrzehnte entwickelt und basiert auf konsequenter Qualitätsorientierung in allen Produktionsprozessen.
Besonders in kritischen Branchen wie Medizintechnik, Automotive und Luftfahrt ist deutsche Fertigungsexpertise gefragt. Hier können Qualitätsmängel schwerwiegende Folgen haben. Deutsche Unternehmen wie die Kunststoffspritzguss-Hersteller Plastro Mayer GmbH, Weidplas GmbH und Gerresheimer AG haben sich beispielsweise als verlässliche Partner etabliert. Sie punkten mit jahrzehntelanger Erfahrung und tiefem Verständnis für komplexe Anforderungen. Als industrielle Zulieferer müssen stehts höchste Standards erfüllt werden.
Vorteile deutscher Kunststofffertigung
Deutsche Hersteller verfügen über einzigartige Stärken, die sie vom internationalen Wettbewerb abheben. Ihre überlegene Qualität und Präzision ermöglichen es, Toleranzen im Mikrometerbereich zu erreichen – eine Fähigkeit, die bei hochwertigen Anwendungen unverzichtbar ist. Diese technische Exzellenz resultiert aus jahrzehntelanger Erfahrung und kontinuierlicher Investition in modernste Fertigungstechnologien.
Ein weiterer entscheidender Vorteil liegt in den kurzen Lieferwegen und der schnellen Kommunikation mit europäischen Kunden. Diese regionale Nähe ermöglicht flexible Reaktionen auf Änderungswünsche und beschleunigt Projekte erheblich. Direkter Kontakt in der gleichen Zeitzone schafft Vertrauen und erleichtert die Zusammenarbeit bei komplexen Entwicklungsprojekten.
Auch die hohe Liefertreue und Planungssicherheit deutscher Unternehmen ist für moderne Produktionskonzepte essenziell. Sie halten Liefertermine zuverlässig ein, was besonders für Just-in-Time-Produktionen unverzichtbar ist. Diese Verlässlichkeit hat sich als Wettbewerbsvorteil erwiesen, da Produktionsstillstände beim Kunden kostspielige Folgen haben können.
Darüber hinaus bieten deutsche Hersteller umfassende Beratungskompetenz durch erfahrene Ingenieure. Diese unterstützen bereits in der Entwicklungsphase, optimieren Designs für die Spritzgussproduktion und reduzieren dadurch Herstellungskosten. Diese ganzheitliche Betreuung schafft langfristige Partnerschaften und Wettbewerbsvorteile.
Herausforderungen für Hersteller
Die Herausforderungen für deutsche Kunststoffhersteller sind vielfältig und betreffen die internationale Wettbewerbsfähigkeit auf mehreren Ebenen. Der massive Preisdruck aus Asien stellt dabei die größte Herausforderung dar. Chinesische und andere asiatische Anbieter produzieren oft 30-50% günstiger, was aus niedrigeren Lohnkosten und weniger strengen Umweltauflagen resultiert.
Gleichzeitig wächst die Konkurrenz aus Osteuropa kontinuierlich. Länder wie Polen, Tschechien und Ungarn bieten eine qualitativ hochwertige Produktion zu deutlich reduzierten Preisen. Diese Anbieter profitieren von ihrer EU-Mitgliedschaft und geringen Transportkosten, was ihre Wettbewerbsposition zusätzlich stärkt.
Deutsche Hersteller kämpfen zudem mit den höchsten Energiekosten weltweit. Auch die steigenden Energie- und Rohstoffkosten belasten die Wettbewerbsfähigkeit erheblich. Kunststoffgranulate werden zunehmend teurer, was die Margen zusätzlich unter Druck setzt.
Obendrauf verstärkt der sich verschärfende Fachkräftemangel diese Problematik. Qualifizierte Werkzeugmacher und Verfahrenstechniker sind schwer zu finden, und der demografische Wandel arbeitet diesem Problem kontinuierlich weiter zu. Dies führt zu steigenden Personalkosten und erschwert die Umsetzung innovativer Produktionskonzepte.
Wie können deutsche Spritzguss-Unternehmen international konkurrieren?
Deutsche Hersteller in der Spritzgusstechnik haben verschiedene Strategien entwickelt, um im internationalen Wettbewerb zu bestehen. Der Fokus auf Hochwertsegmente erweist sich als besonders erfolgreich. Sie konzentrieren sich auf komplexe Teile mit hohen Qualitätsanforderungen, wo sie ihre Stärken ausspielen und angemessene Preise durchsetzen können. Zusammen mit einer Spezialisierung auf Nischenmärkte sind hier gute Chancen geboten. Kleine Losgrößen und Sonderanfertigungen sind für Großhersteller teilweise uninteressant, aber deutsche Mittelständler können hier profitable Nischen besetzen. Diese Strategie ermöglicht es, sich vom reinen Preiswettbewerb zu lösen und Mehrwerte zu schaffen.
Automatisierung und Effizienzsteigerung spielen ebenfalls eine zentrale Rolle in der Wettbewerbsstrategie. Moderne Robotertechnik und vollautomatische Fertigungslinien reduzieren Personalkosten erheblich. Gleichzeitig steigt die Produktionsgeschwindigkeit bei konstanter Qualität, was die Wettbewerbsfähigkeit verbessert. Die mit einhergehende Digitalisierung der Produktionsprozesse revolutioniert die Fertigung zusätzlich. Industrie 4.0-Technologien ermöglichen präventive Wartung und Echtzeitoptimierung, was die Effizienz steigert und Ausschuss reduziert. Diese technologischen Vorsprünge schaffen nachhaltige Wettbewerbsvorteile.
Technologien deutscher Spritzguss-Betriebe
Deutsche Spritzguss-Betriebe setzen auf modernste Technologien, um ihre Wettbewerbsfähigkeit zu sichern:
- Mehrkomponentenspritzguss für komplexe Bauteile ermöglicht die Kombination verschiedener Materialien in einem Arbeitsgang. Diese Technologie eröffnet neue Anwendungsbereiche und Geschäftsmöglichkeiten.
- Reinraumproduktion für Medizintechnik-Anwendungen ist ein weiterer Bereich, in dem deutsche Unternehmen kontinuierlich investieren. Sterile Fertigungsbedingungen sind für medizinische Anwendungen unverzichtbar und erfordern höchste technische Standards sowie entsprechende Zertifizierungen.
- Digitale Prozessüberwachung in Echtzeit gewährleistet gleichbleibende Qualität und minimiert Nacharbeit. Sensoren überwachen jeden Spritzvorgang und erkennen Abweichungen sofort. Diese Technologie ist entscheidend für die Qualitätssicherung und Effizienzsteigerung.
- Intelligente Werkzeugtemperierung verkürzt Zykluszeiten und verbessert die Bauteilqualität erheblich. Präzise Temperaturkontrolle ist für optimale Produktionsergebnisse unerlässlich. Moderne Systeme passen sich automatisch an verschiedene Materialien an und optimieren den Fertigungsprozess kontinuierlich.
Deutsche Unternehmen investieren stark in Forschung und Entwicklung, um ihre langfristige Wettbewerbsfähigkeit zu sichern. Ihre Innovationskraft zeigt sich u. a. in der Entwicklung neuer, biokompatibler und recycelbarer Materialien, die neue Märkte erschließen. Gleichzeitig verändert Industrie 4.0 mit vernetzten, selbstoptimierenden Maschinen die Produktionsprozesse grundlegend und steigert Effizienz sowie Flexibilität. Ergänzend verbessert Künstliche Intelligenz die Qualitätssicherung, indem sie Wartungsbedarfe vorausschauend erkennt und ungeplante Stillstände reduziert – was die Produktivität deutlich erhöht.
Standort Deutschland: Qualität als Differenzierungsmerkmal
Deutsche Kunststoffhersteller positionieren sich bewusst als Qualitätsführer – eine Strategie, die sich besonders in anspruchsvollen Märkten auszahlt. Vor allem die Medizintechnik vertraut auf deutsche Präzision bei kritischen Anwendungen. Implantate, Operationsinstrumente und Diagnostikgeräte erfordern höchste Genauigkeit, hier ist "Made in Germany" oft alternativlos.
Auch die Automotive-Industrie schätzt die Zuverlässigkeit deutscher Hersteller besonders bei sicherheitskritischen Komponenten. Fahrzeugteile müssen jahrelang fehlerfrei funktionieren, eine Kompetenz, die sich deutsche Hersteller über Jahrzehnte erarbeitet haben. Diese Expertise ist schwer zu replizieren und schafft nachhaltige Wettbewerbsvorteile.
Auf bewährte deutsche Partner wird auch in der Luftfahrt-Branche gesetzt. Flugzeugbauteile unterliegen strengsten Zertifizierungen, und etablierte deutsche Zulieferer verfügen über die nötigen Zulassungen und Erfahrungen. Diese Markteintrittsbarrieren schützen vor neuen Wettbewerbern.
Fachkräfte und Ausbildung als strategischer Vorteil
Das duale Ausbildungssystem ist ein einzigartiger Standortvorteil deutscher Unternehmen. Praxisnahe Ausbildung schafft hochqualifizierte Fachkräfte, die international geschätzt werden. Diese präzise Ausbildung schafft Expertenwissen in der Tiefe. Werkzeugmechaniker und Kunststofftechniker lernen drei Jahre lang alle relevanten Fertigkeiten, eine Ausbildungstiefe, die andere Länder selten erreichen.
Kontinuierliche Weiterbildung hält das Wissen aktuell und sorgt für die schnelle Umsetzung technologischer Entwicklungen in die Praxis. Regelmäßige Schulungen und Zertifizierungen gewährleisten, dass die Mitarbeiter auf dem neuesten Stand der Technik bleiben.
Zusätzlich fördern Kooperationen mit Hochschulen Innovation und bringen neue Erkenntnisse direkt in die Anwendung. Gemeinsame Forschungsprojekte ermöglichen es, dass Studenten bereits praxistaugliche Lösungen entwickeln. Diese enge Verzahnung von Theorie und Praxis ist ein wichtiger Erfolgsfaktor.
Fazit: Zukunft Made in Germany
Indem sie konsequent auf Qualität, Innovation und Kundennähe setzen, können deutsche Hersteller ihre Zukunft sichern. Der Fokus liegt klar auf hochwertigen, komplexen Anwendungen statt auf Massenproduktion, die zunehmend ins Ausland verlagert wird. Investitionen in neue Technologien und Verfahren sind dabei unerlässlich, um im internationalen Wettbewerb die Spitzenposition zu behaupten. Unternehmen, die den Wandel aktiv mitgestalten, gelten als die Gewinner von morgen.
Zusätzlich bietet die branchenweite Zusammenarbeit großes Potenzial: Gemeinsame Forschung und Entwicklung ermöglichen effizientere Ressourcennutzung und stärken die Wettbewerbsfähigkeit. Wer Tradition mit Innovation verbindet, positioniert sich erfolgreich am Markt – und hält das Qualitätsversprechen „Made in Germany“ auch in Zukunft lebendig.
Die Plastro Mayer GmbH steht exemplarisch für die Innovationskraft des deutschen Mittelstands im internationalen Wettbewerb. Als Allround-Anbieter liefert das Unternehmen Komplettlösungen aus einer Hand – von der Spritzgussfertigung bis zur Endmontage. Diese durchgängige Produktion unter einem Dach ermöglicht effiziente Prozesse, minimiert Schnittstellen und garantiert eine gleichbleibend hohe Qualitätskontrolle. Besonders in der Medizintechnik zeigt sich die Spezialisierung: Hier fertigt Plastro Mayer hochpräzise Komponenten mit besonderem Know-how und setzt auf kontinuierliche Automatisierung durch moderne Roboterzellen, um die Produktivität zu steigern und Kosten zu senken.